Choice Is the New Black
How craft, data and robotics are reshaping quality.
A lot has changed since Henry Ford said, “Any customer can have a car painted any color that he wants as long as it’s black.” As organizations evolve their cultures to meet new employee needs, they want modern office chairs, desk systems and other products that are unique. Today, choice is the new black. Lots of choice.
But, is it possible for mass-scale manufacturing to create the goods consumers and organizations are seeking? We think so. In large part because we are learning how to behave like crafters—on a large scale.
But what impact will increased choice have on manufacturing and quality? We knew Steelcase Vice President of Global Operations Robert Krestakos would have some interesting things to say on the topic. And while we had his attention, we asked about the role technology is playing in quality today and what we can expect down the road.

360: What does consistency look like in a maker movement environment where customers want to put their own signature on spaces?
Robert Krestakos: Making is a privilege. We all genuinely feel this way at Steelcase. Sure, we have to bridge the gap that exists between the world of high-end, high-volume, scale-based manufacturing and the demand for the truly distinctive, individual and bespoke. But we approach the task with a sense of optimism and craftsmanship.
Today, it’s about much more than being able to offer lots of colors and configurations. I think quality means you design and engineer for predictable and consistent outcomes, but that doesn’t have to mean you make the same thing with little or no variation. In our industry, there’s enormous complexity in the logistics of getting products to our customers in a complete, on-time, and damage-free manner. Using math and science is key to managing that complexity. Our data-driven tools and capabilities give us creative freedom and engineering flexibility. They allow us to be more predictive; we can look at a lot of different design options and know immediately whether or not we’re on firm ground from a quality and life-cycle standpoint. Then, with confidence, we can layer scalability and agility onto that. Processes can be—and are—designed to allow for a wide range of configurations yet still be extremely consistent in how they work.
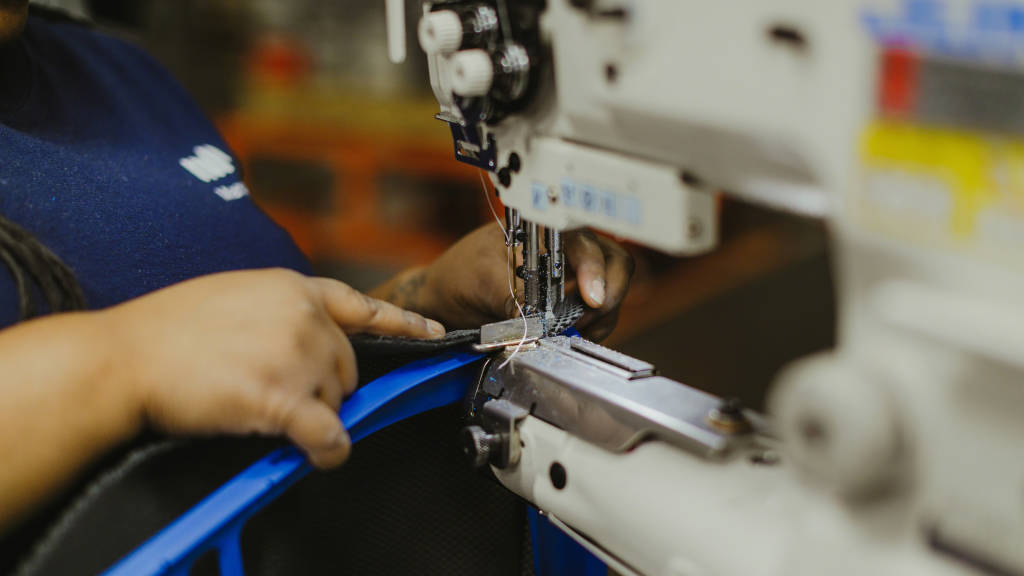
360: How do you create that agility?
RK: First, we have to realize we’re playing by a different set of rules. Today, we have to have processes that allow us to be nimble and make fast decisions. But, at the same time, we have to mitigate risk and keep products affordable. We have to think about things like whether a supplier is a normal part of our scale-based supply chain, or if the supply will be needed only for a specific need on the craft-based part of our business.
And how do we handle certification and liability and warranty? How is it packaged? Packaging engineering and manufacturing engineering and industrial design are all different disciplines. There has to be a high degree of coordination. We have to think about a complete solution, even for a one-time order. And we want to retain, when we can, some of the inherent advantages of our volume and ability to scale.
360: Why is volume and scalability important to a customer?
RK: One obvious benefit is lower cost. Our decades of experience and research allow us to share proven parts and materials across multiple products. The Steelcase Series 1 chair is a good example. The lightweight, compact chair incorporates many of the same performance, style, functionality and choice features of other chairs, but at a lower price. All that capability doesn’t go away when we produce a less expensive option for our customers. Our heritage and our holistic thinking come into play with everything we build.
360: Technology has to be part of almost any conversation today. Is there risk there or all reward?
RK: Data is, no doubt, driving manufacturing. In a world of advanced technology and big data, the ability to be more accurate about predicting failure points will be dramatically enhanced through simulations and data analysis. Will that capability replace the need for physical testing? Perhaps one day. In the foreseeable future, it will most certainly be an important complement to traditional approaches.
Important to note, too, is that we’re making big jumps in the production process through the Industrial Internet of Things (IIoT). It’s really changing the roles of people on the plant floor. For example, zone leaders are getting access to real-time data about how production activity is going and can make ongoing adjustments. And sensors can be deployed in various ways to watch for anomalies in our execution. If the settings for machine tolerances on certain equipment starts to change, the IIoT can alert someone before it becomes a problem in the part we’re making. We call this the Voice of the Process (VoP).
Our data-driven tools and capabilities give us creative freedom and engineering flexibility.
We’re applying big data—data that before IIoT, we didn’t have—and doing analytics in more disciplined and rigorous ways across the board, looking for patterns that lead us to root causes and finding ways to get quality further upstream into the development and engineering process. It all makes our jobs easier.
360: Robotics is an exciting and changing area of technology. What about the concern, though, that robotics will displace workers?
RK: Our approach with technology always will be to add customer value and augment our performance. It’s possible that certain technologies could change the nature of work and make some types of work obsolete, but that’s nothing new and that’s not our main goal. We want to find better ways of working that improve our products from an aesthetic, quality and cost standpoint. Technology could very well add jobs in some cases.
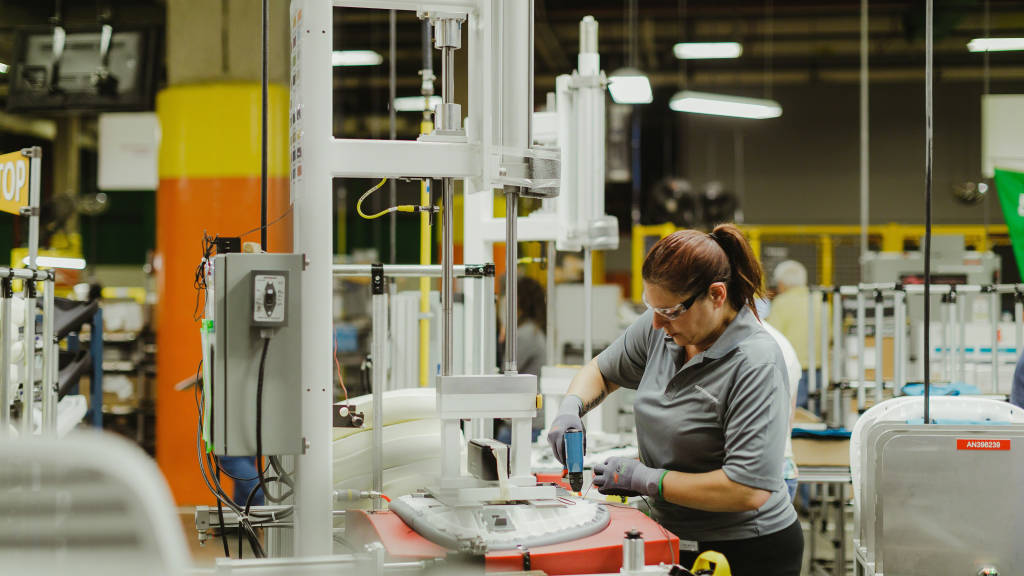
360: A few final words about what the future might hold?
RK: When we say “our quality is in the details,” we’re not talking singularly about product quality. We’re talking about the entire experience of doing business with us—from placing an order and having it go through the plan, source, make and deliver phases, to getting the order all the way to the customer and changing it, if necessary, at any point in the process. It all counts. And expectations will only increase next year, and the year after that—which, to me, is exciting. There is pride that comes with making something when there is an elevated level of difficulty and skill involved, and when all the pieces come together.
To hear more about how new approaches to quality and modern craft are influencing design at Coalesse, listen to the 360 Real Time podcast, The Evolution of Quality and Craft.