Le Lab du MIT et Steelcase redéfinissent l’impression 3D
Le Self-Assembly Lab du MIT, Steelcase et le designer déjà primé, Christophe Guberan, ont collaboré à la création d’un nouveau processus d’impression 3D dévoilé lors de la semaine du design à Milan. Supprimant les trois contraintes de l’impression 3D traditionnelle, cette technologie améliore la vitesse, la taille et la qualité grâce à une technique d’impression liquide rapide. Le partenariat du MIT avec Steelcase et Christophe Guberan a pour objectif d’explorer l’avenir de la personnalisation du mobilier et les possibilités de customisation à travers l’innovation.
POURQUOI PERSONNALISER ?
Partout dans le monde, les gens rejettent le bureau stéréotypé et monolithique créé par leurs employeurs. De nombreuses entreprises s’aperçoivent en effet qu’elles doivent repenser leur espace de travail pour offrir une expérience plus centrée sur l’humain qui permettra d’attirer et de retenir les talents hautement qualifiés tout en améliorant le bien-être et l’engagement de leurs employés. Les environnements de travail qui offrent la possibilité de personnaliser le mobilier permettent d’accroître le sentiment d’appartenance et de favoriser l’expression personnelle et l’authenticité.

QUOI DE NEUF ?
L’impression tridimensionnelle existe depuis des décennies. Mais elle s’accompagne toujours d’un certain nombre de contraintes. La création d’objets nécessite l’utilisation d’une structure de support, la superposition de couches de matière et un temps de séchage. Du fait de ces exigences, le procédé est donc voué à la lenteur, à une application limitée à de modestes projets et à une faible qualité. Fondé par Skylar Tibbits, professeur adjoint au MIT, et codirigé par Jared Laucks, le Self-Assembly Lab a pour objectif de mettre au point un nouveau procédé qui améliore la vitesse d’impression, ainsi que la taille et la qualité du matériel obtenu.
« Il est essentiel pour nous de nous associer à des partenaires de l’industrie », déclare Skylar Tibbits. « Ils apportent des connaissances, des problématiques, une pertinence et une expertise de leur domaine que nous ne possédons pas. »
Après des mois de collaboration avec Steelcase sur ce projet, une nouvelle technique innovante a ainsi vu le jour. Le processus d’impression se déroule dans un gel, ce qui permet à un designer de dessiner dans un espace tridimensionnel sans subir les contraintes de la gravité. En l’absence de matériel et structure de support traditionnels ou même de superposition de couches, le processus d’impression est plus rapide et permet de créer un objet dont la taille ne sera limitée que par celle de la machine. Le processus reposant sur le mélange de deux substances permet également de sécher chimiquement le matériau plutôt qu’à l’aide d’un dispositif utilisant la lumière ou la température. La technique utilisée mélange et sèche à mesure que s’exécute l’impression 3D.
RAPID LIQUID PRINTING (IMPRESSION LIQUIDE RAPIDE)
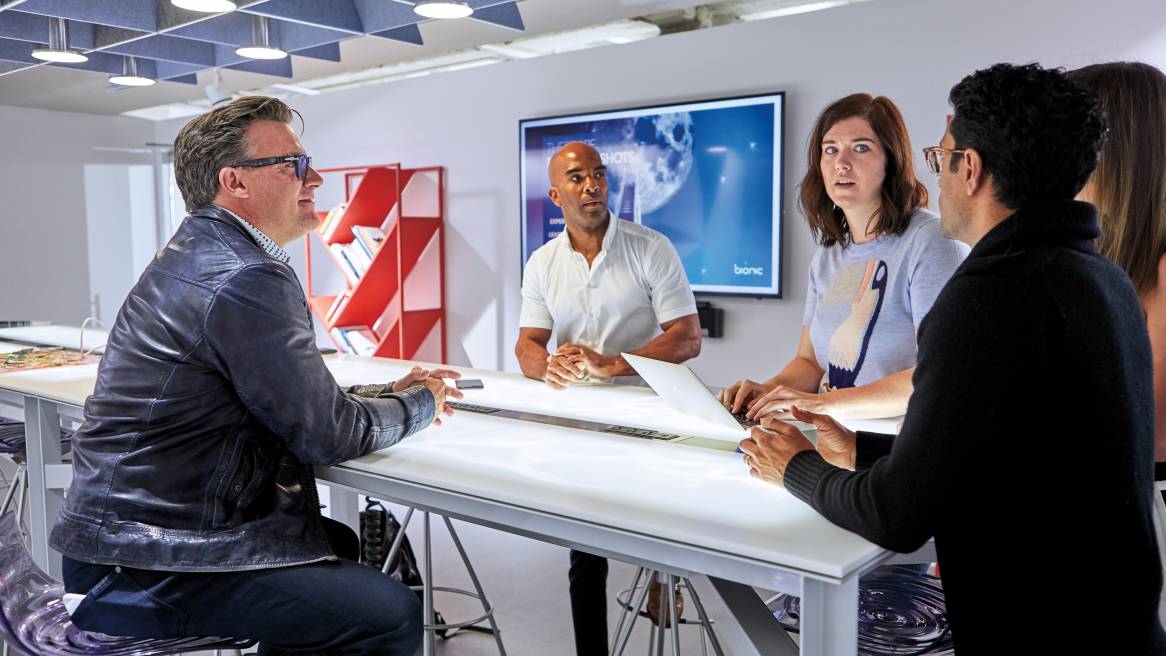
Lors de la semaine du design de Milan, le Self-Assembly Lab du MIT et Christophe Guberan ont révélé les coulisses de la création d’un plateau à l’aide de ce processus d’impression 3D révolutionnaire. Skylar Tibbits a expliqué qu’il fallait environ 28 minutes pour imprimer le design complexe du plateau de la table Bassline. Lors d’une autre expérience, l’équipe a réussi, grâce à la technique du Rapid Liquid Printing, à imprimer en 10 minutes une structure dont la création nécessitait auparavant 50 heures avec un autre procédé d’impression 3D. Le design, le matériau et la taille sont autant de facteurs qui affectent la vitesse d’impression.
ET ENSUITE ?
Ce nouveau procédé d’impression, bien qu’expérimental pour l’instant, montre le potentiel lié à l’utilisation future d’une catégorie de matériaux ayant les mêmes propriétés que des produits du monde réel.
« Pour un designer, ce qui est absolument fascinant et unique avec le Rapid Liquid Printing, c’est la qualité de ligne de l’impression. C’est souple, presque organique. Cela évoque des images de coups de pinceau ou des branches de végétaux », affirme Yuka Hiyoshi, dessinateur industriel chevronné travaillant chez Turnstone. « La vitesse d’impression est très impressionnante. Dans un avenir lointain, les objets de grande taille pourront être imprimés en quelques minutes au lieu de plusieurs jours. De plus, cette technologie n’est pas limitée aux matériaux classiques de l’impression 3D, ce qui la rend très appréciable du point de vue du design. »
La collaboration de Steelcase avec le MIT permettra de continuer à chercher de nouvelles réponses concernant les matériaux, les formats d’impression et l’amélioration des procédés. Il sera également important de déterminer le produit ou l’objet le plus adapté à ce type d’impression, celui à qui ce nouveau procédé profitera le plus.
Partenaires de recherche de longue date, Steelcase et le MIT possèdent un parcours commun riche d’explorations de ce que sera l’espace de travail de demain. Si leur travail est encore en phase d’exploration, cette collaboration n’en est pas moins une réponse adaptée à la nécessité pour les environnements de travail d’offrir des espaces plus informels, plus authentiques ainsi que produits et expériences uniques.