Making a positive impact on the world
How the Steelcase plant in Rosenheim is helping both people and planet
Steelcase’s commitment to sustainability is tangible not only in a global context. It is also reflected in the local initiatives of dedicated employees who are passionate about their work, their plant, their employees, and the environment. The Steelcase plant in Rosenheim, Bavaria, managed to implement several sustainability projects in a short period of time.
Local sustainability initiatives at the Rosenheim plant
In 2020, the Steelcase plant in Rosenheim introduced sustainability as a new strategic operational pillar alongside safety, quality, delivery, and cost. The timing could not have been better – the cost of solar panels and combined heat and power systems (CHP), also known as cogeneration, had decreased significantly. And the wood boiler, in operation since 2000, was no longer up to date with respect to energy efficiency. Therefore, the Rosenheim plant decided to implement corresponding initiatives in the same year: In addition to several other small initiatives, a photovoltaic system, a combined heat and power plant to replace the wood-fired boiler, and a new carton cutting unit that contributes to the reduction of packaging waste were put into operation, which contributed significantly to the optimization of process efficiency.
1. Photovoltaic Plant
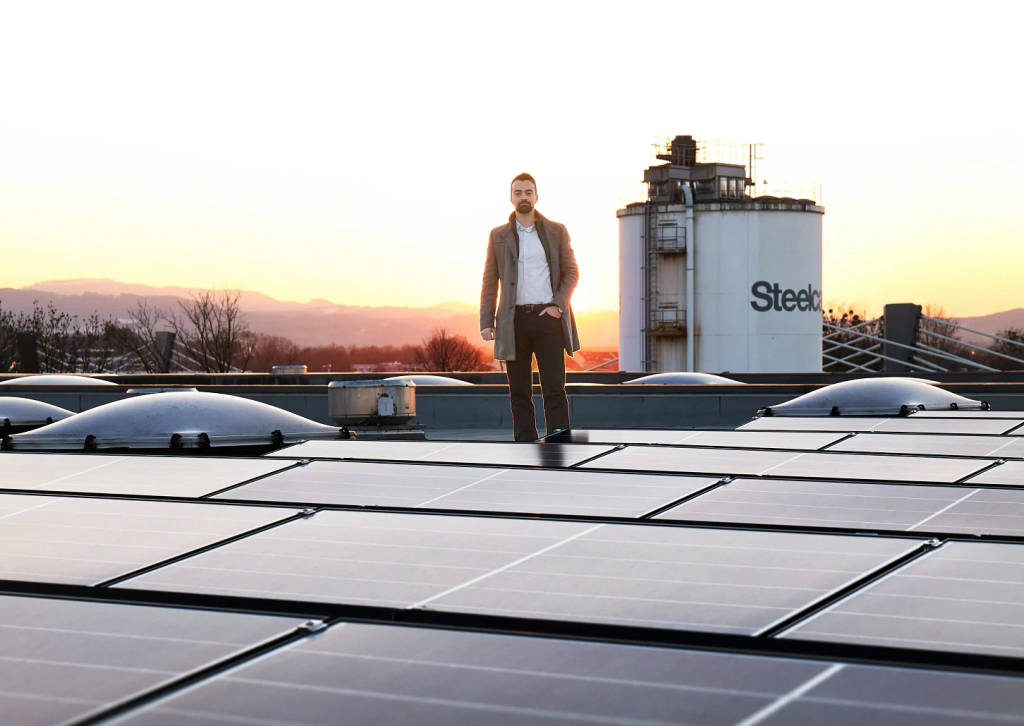
“The solar panels measuring 250 m2 produce 30.000 kWh of electricity per year. When paired with the combined heat and power system, the Rosenheim Plant can produce about 50% of the plant’s electricity requirements in the winter.“
Cristian BokorPlant Manager Rosenheim
In 2020, the plant’s previously unused roof was equipped with a photovoltaic plant of approximately 250 m2, which produces an output of 25 kW on sunny days. Cristian Bokor, plant manager in Rosenheim, explains: “The solar panels measuring 250 m2 produce 30.000 kWh of electricity per year. When paired with the combined heat and power system, the Rosenheim Plant can produce about 50% of the plant’s electricity requirements in the winter.“
2. Optimization of packaging
Apart from the photovoltaic system and the CHP unit, the Rosenheim plant improves its ecological footprint with smaller but equally important initiatives, above all in packaging and the elimination of plastics. For instance, substituting a foil material used for packaging brought the level of post-consumer recycled material up to 35%. Eliminating plastic in inventory management also promotes more resource-efficient use of materials. The purchase of a carton cutting unit reduces the total amount of waste and allows the plant to be more independent. This is an advantage, especially in the current period of continuous supply chain disruptions, as it ensures uninterrupted operation of the plant.
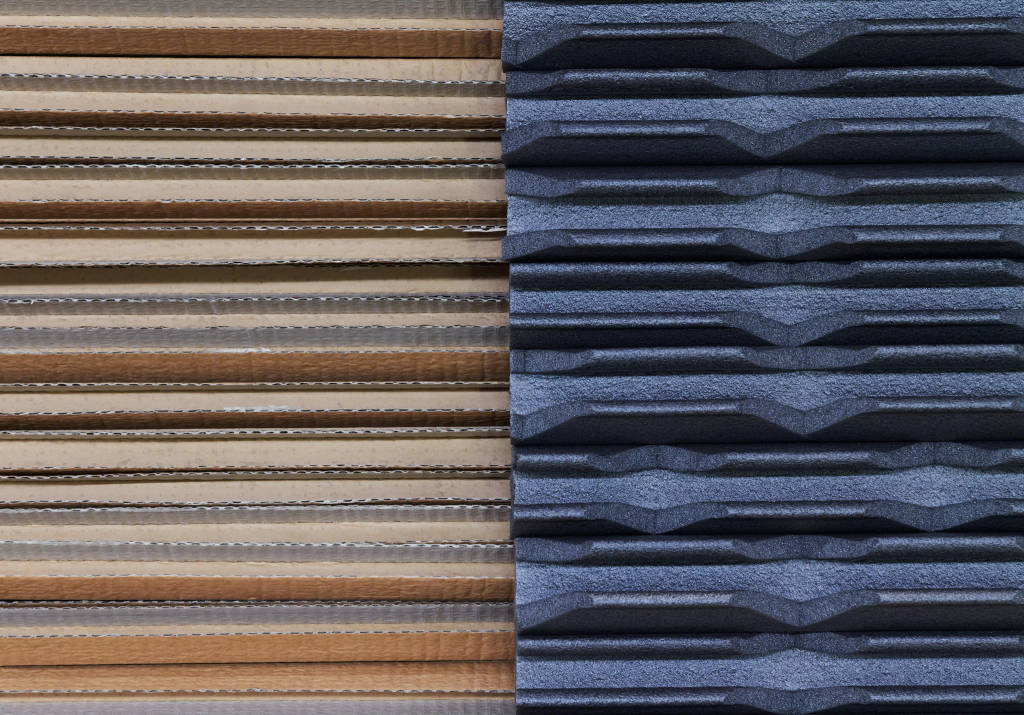
The Rosenheim leadership team is constantly exploring new, resource-efficient options and testing new packaging solutions to determine, among other things, whether these influence product quality. For example, cardboard can be very abrasive on painted or textured plastic surfaces, which means that plastic bags or foam films are often used to protect products from damage and abrasion. Supplying a replacement product due to inadequate packaging in turn will require the use of natural resources such as raw materials, water, waste, and energy. To find solutions to these complex issues, the Rosenheim plant has a task group focusing specifically on optimizing packaging options, as this topic is one of the most important factors in reducing overall waste.
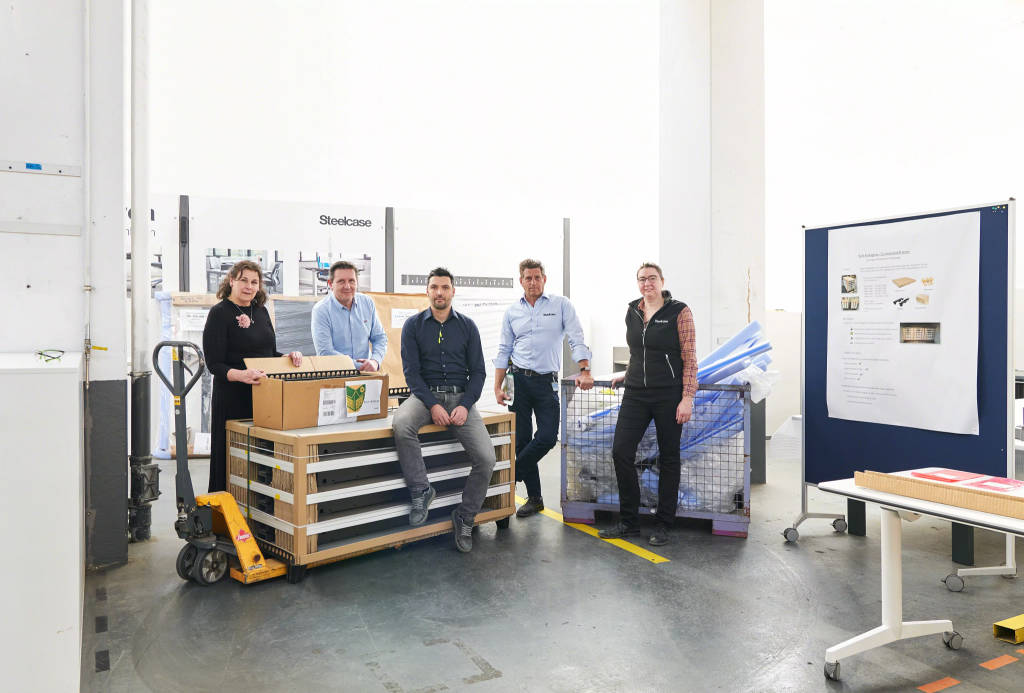
3. Advanced technology – Combined heat and power
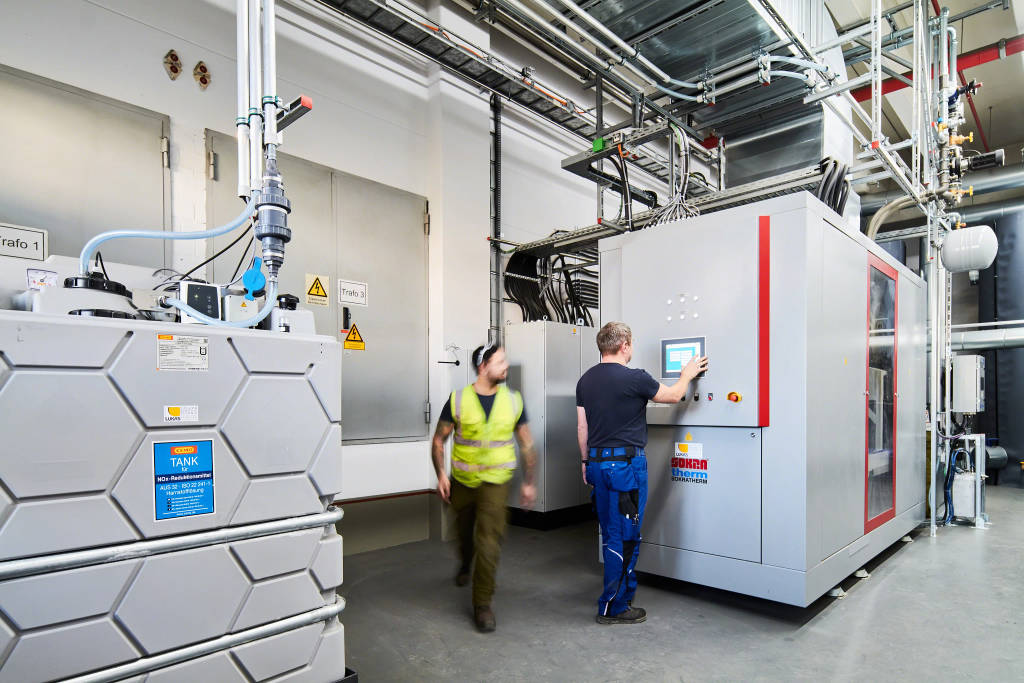
Combined heat and power systems have become popular in Germany for being proficient in producing electric power and thermal energy. CHP units combine power and heat (combined heat and power, or CHP in short), generating heat as well as electricity. The electricity is either used directly for running processes or fed into the local power grid. The heat generated during the combustion of the fuel is first stored in a buffer tank and is then available for production. One way we utilize the thermal energy generated from our CHP system for production is within our paint line washing process where water is efficiently heated to optimal temperatures of 50 to 60 degrees. The hot water is supplied by the CHP unit in a particularly economical and environmentally friendly way. The additional use of the urea-based Ad Blue catalyst, a product renowned for its use in the automotive sector, substantially reduces nitrogen emissions. The innovative CHP technology can also be easily switched over to a hydrogen fuel source as infrastructure becomes available.
4. Water conservation measures
Steelcase’s sustainability goals also include efficient water management to reduce global water consumption in operations and control the quality of wastewater. The Rosenheim plant uses a Vacudest system to purify water from metal washing processes by separating distilled water from contaminants. The cleaned water is then fed back into the processes. This vaporization method has been used at the Rosenheim plant for more than 15 years. The plant effectively recovers 97% of the wastewater while the remaining 3% are collected as sewage sludge and regularly transferred to a licensed treatment facility.
Sustainability Pioneers

“In the long term, we are particularly interested in expanding our collaboration with marketing and design to achieve even greater environmental protection at the product level, e.g., to address sustainability aspects and circular economy even more intensively during the conception and brainstorming phase.“
Cristian BokorPlant Manager Rosenheim
The sustainability initiatives put in place by the small management team at the Rosenheim plant – solar installation, CHP, and packaging optimization – show that a lot can be achieved in a short time when it comes to sustainability, especially with the help of resolute employees, such as the ones in Rosenheim. The core team in Rosenheim is actively exchanging information with other European and global Steelcase plants to learn about the local environmental protection measures and to pass on the knowledge and experience they gained over the last two years regarding solar energy technology and the CHP plant operation. “We demonstrated that environmental protection measures can be implemented at a local level and are also feasible in terms of economic efficiency,” says plant manager Cristian Bokor. “At the moment, we are exploring the possibility of expanding the solar power system. In the long term, we are particularly interested in expanding our collaboration with marketing and design to achieve even greater environmental protection at the product level, e.g., to address sustainability aspects and circular economy even more intensively during the conception and brainstorming phase.“
Steelcase‘ global environmental goals
Steelcase has a long-standing commitment to environmental protection, and we are documenting our commitment as transparently as possible. In addition to achieving carbon neutrality in our own operations, we have committed to reducing absolute emissions at our sites by 50% by 2030. We are working relentlessly to minimize the environmental impact of new products from the design stage onwards, and to move further and further towards a circular economy. This approach has resulted in the development of Perch, our most sustainable product, which consists of 70% recycled material and is 100% recyclable.
Most of our products, materials and even production sites are independently certified according to a range of sustainability standards.
We regularly receive awards for our commitment to combating climate change and protecting the environment. However, our commitment to sustainability and the environment does not just show in management-driven, company-wide actions, but is purposefully advanced by committed employees at the local level.
Learn more about the Steelcase perspective on these activities in our latest Impact Report, which transparently details all of our sustainability and environmental initiatives.