Pushing Possibilities
MIT’s Self-Assembly Lab shatters the barriers of 3D printing
Google the name Skylar Tibbits and you’ll find TED Talks on creating things that make themselves without humans or machines. Intrigued? Type his name into YouTube and see for yourself.
Components spontaneously assemble into structures. Materials reconfigure, go from liquid to solid and act like actuators.
As founder and co-director, along with Jared Laucks, of the Massachusetts Institute of Technology’s (MIT) Self- Assembly Lab Tibbits and team’s exploration into melding design of the physical and digital worlds has produced numerous innovations that appear mind-blowing to the untrained eye. One of the Self-Assembly Lab’s latest experiments, in partnership with Steelcase and designer Christophe Guberan, broke the three main constraints of 3D printing: speed, scale and material properties. They created an intricate lattice tabletop for turnstone’s Bassline table.
Tibbits and team, Steelcase and Guberan asked: Can we print a chair in minutes? A chair, most likely. A tabletop, most definitely—28 minutes in fact. The team successfully developed a new 3D printing technology called rapid liquid printing. This technology prints a design through drawing in 3D space within a gel suspension and enables the incredibly fast creation of large scale, customized products with high-quality materials.
“Execution and implementation of 3D printing has been limited by three main factors,” Tibbits describes. “One of them is speed: Printing tends to be slow compared to other industrial processes. The second is scale: Printing is usually fairly small scale. The third is material properties: Printing today tends to have low quality materials.” According to Tibbits, rapid liquid printing is the perfect example of design and manufacturing changes symbiotically working together, an area of exploration that the Self-Assembly Lab continues to push.
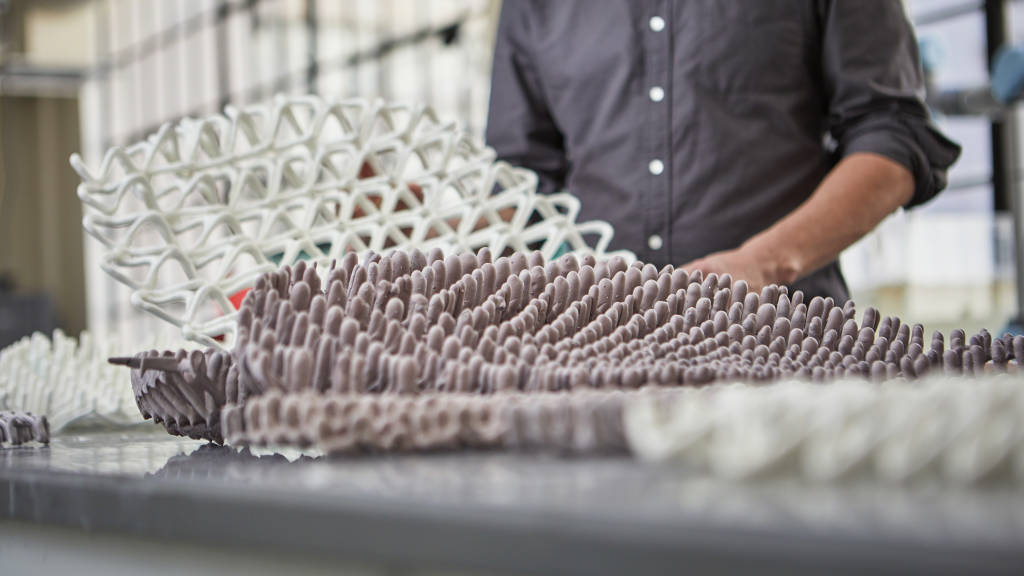
“I think creativity is about experimentation and research. Our goal is to push the boundaries of what’s possible and invent things that weren’t possible before,” says Tibbits. To stay inspired, the lab, made of students and researchers from many different backgrounds, constantly critique themselves. “Every time we do a project there are ten new ideas for new projects and those projects make the previous ones obsolete. We say, we need to make it smarter, faster, better; it needs to have less complexity, but more functionality.”
A crucial element to creativity for the Self-Assembly Lab is collaboration; their work show openness to collaborate with many different industries and disciplines. “The collaboration with Steelcase is really the perfect synergy between our research and really pushing the envelope of what’s possible, as Steelcase is the leader in space and interested in what’s next for materials, human comfort and new manufacturing principles,” notes Tibbits.
“Every time we do a project there are ten new ideas for new projects and those projects make the previous ones obsolete.”
Skylar TibbitsDesigner & Computer Scientist, MIT
After one month of intense development, the 3D printed Bassline tabletop went from concept to a tangible industrial furniture piece. This rapid iteration was fostered by using printing as a “design fabricator,” Tibbits explains. “Design can emerge through the process of making and a new design language can form. Functionality can emerge in the same way.”
As the Self-Assembly Lab continues to advance what’s possible in new construction systems, manufacturing processes and material properties, they continue to find new quests to conquer. “We’re really on more of a quest of exploration than a specific vision,” says Tibbits. “We operate on things like surprise. How do we surprise ourselves? How do we break things, test things and design through making?”
No one knows, but the world will be watching.
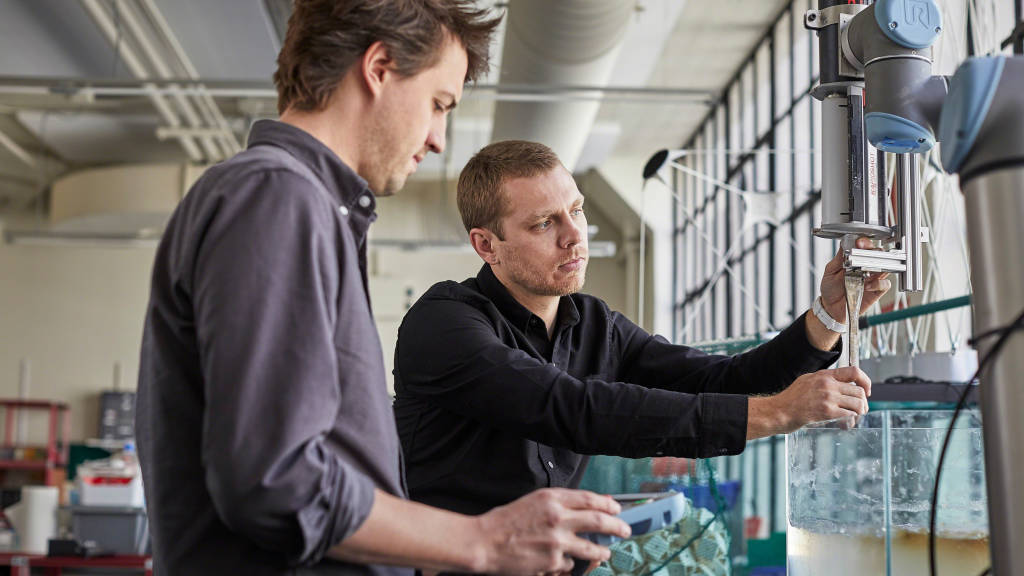